Agriculturalists Learn About Soil Moisture Sensors By Doing DR. JOE HENGGELER
PORTAGEVILLE, MO.
Participants at University of Missouri’s annual Crop Injury and Diagnostic Clinic held at the MU Bradford Farm near Columbia, Mo. had a chance to teach the teacher. In the session titled “Wireless Irrigation Sensor Management”, taught by Dr. Joe Henggeler from the MU’s Fisher Delta Research Ce-nter in Portageville, class participants in each of the three sessions were divided up into groups of three to five. They were given a foam board model of a center pivot irrigation system and a set of colored push pins. The pins represented soil moisture sensors buried at depths ranging from one to five foot, automatic rain gauges, and field data loggers. Student teams were then challenged to design a soil moisture monitoring system for the center pivot, by locating where they would place sensors at and at what depth.
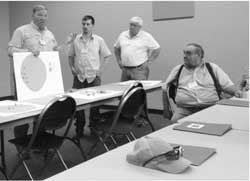
Prior to unleashing them, Henggeler had instructed the group on the fundamentals of wireless sensor technology, including economic considerations. For example, both initial system and annual costs depend on how and where the collected field data is to be retrieved and stored. The order of the least to the most expensive options are: manually downloading the data from a data logger at the edge of the field, using Radio Frequency signals to send collected data to one’s own PC, and, finally, using a cell or satellite modem to transfer information from the field data logger to a commercial data management platform on the web.
The cost and expected life of the various equipment components were provided to the students; then they were split into small groups and the teams challenged to design a system that would adequately monitor the soil moisture status of their pivot, while keeping total investment costs to less than $2,800 and annualized costs less than $10/acre/year (Fig. 1). Each team then reported back to the whole group on their design (Fig. 2), explaining why they chose their design and what the initial and annualized costs were. The other groups could then ask them questions or comment on their design.
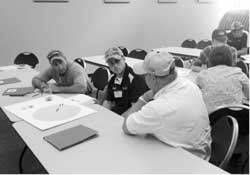
Fig. 1. One of the teams at the workshop discussing
the placement and number of monitoring sites, and if
the total cost would be something a real pivot owner
might be amendable to.
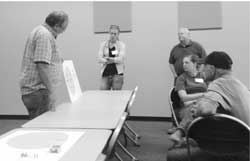
Fig. 2. Tim Reinbott, superintendent of the MU Bradford Farm,
makes the presentation for his team to other session attendees.
The background in irrigation of the students varied from none to having previously worked with an irrigation company. The groups brought a lot of common sense to the project, for instance, many opted to having their pivot design service a shallow clay-pan soil, common in central Missouri, and so they elected to monitor the moisture in just the top foot. Field-scouting expertise of some of the team members came to the forefront by choosing locations in their design that would both be easily accessible and well-marked. However, most of the groups scattered their sensor sites around the pivot. Only one group thought to install their sensor locations so that they would lay in a straight line radiating from the center of the pivot. Doing so would have it that all the sensors were watered at the same time. Scattering sensors would mean that some sensors would have just been wetted, while others a day or week before. It would be confusing to try and average sensor values that weren’t watered simultaneously.
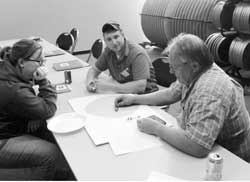
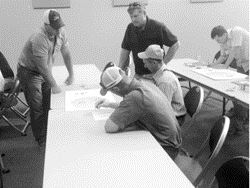
Challenging the students to think about and discuss their ideas with others in their small break-away groups and then coming up with their own design – it was thought – was a better way to learn about placement of sensors, data loggers, and economic concerns then by a moderator just flipping through a few PowerPoint slides on the topic.
Henggeler came up with the idea of using a model from work he had done with irrigators 40 years before while a Peace Corps Volunteer (PCV), where he worked as an irrigation extension agent in Sierra Leone (Fig. 1). PCVs in that west African country were teaching rice growers, who used the slash-and-burn method on steep hillsides, which entailed going to a different site and starting over every year (not to mention the severe environmental problems of erosion), that they could instead farm, year after year in the same spot if they would cultivate the swamps that snaked between the hills, once they cleared them and put in damming and drainage structures. The swamps were only about 100 yards wide but would meander for miles and miles. Since Sierra Leone gets almost 100 inches of rain a year, inland paddies could be irrigated with caught rainfall moving down the swamp. The swamps were naturally lower in the center, with land surface elevations rising on either side. The central water way at the head of the field serving both as the supply ditch and the drainage ditch, was dammed up so that water could be diverted to the outside edges of the field where it was introduced into the paddy and then recollected in the drainage ditch.
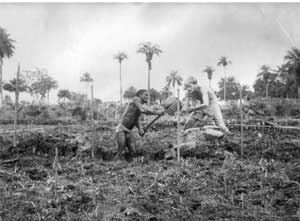
Fig. 3. Joe Henggeler working with one of his farmers on constructing
the central water way in his future rice farm. The head dike that diverts
the swamp’s stream of water to the outside edges of the field is already
constructed and can be seen at the top of the field.
To show farmers how this worked he got a piece of plywood and used clay to build a scale model of a section of swamp farmland that had bunds around the paddies and a central waterway. Running water from a small container at the top of the model, farmers could play with damming the top and bring water in from the sides to be collected back into the central drainage ditch. Farmers quickly caught on to what needed to be done in their swamps. Forty years later, Henggeler could use Google Earth and see that those systems are still in use today. ∆
DR. JOE HENGGELER: Irrigation Specialist, University of Missouri
|
|