Do You Need 12-Inch Column Pipe For Your Wells?
PORTAGEVILLE, MO.
For the irrigation world, the
old adage “desperate
times, call for desperate
measures”, might be rephrased
to read: “big fuel
costs, call for big pipe sizes.”
The point being, that with the
high flow rates common in the
SE Missouri area and today’s
price of energy, we need to make sure the column
pipe we are installing in our wells is not
wasting too much energy from excessive friction
loss occurring because the pipe size is too small.
Indications show that in some instances we may
need to move up to 12-inch column pipe, even if
it means drilling a 16-inch well versus a 10- or
12-inch one.
Irrigation wells consist of the outer casing pipe,
normally made of PVC, and the inner column
pipe, normally made from steel. The water travels
up the column pipe, so it is in the column
pipe that friction loss occurs. Typically, column
pipe size is either 8 or 10 inches. Pumps are typically
set at 60 feet, so friction occurs during this
brief sojourn to the surface. However, if the
pump has an intake pipe on the bottom end, say
ten feet long, then friction loss will occur there
also, thus friction occurs along 70 feet of pipe in
this instance. Obviously, the longer the length
of pipe, the more the amount of friction loss will
be.
Here is why we may be needing bigger column
pipe sizes: as flow rates increase, the friction
loss goes up. Actually, friction loss is related to
the velocity the water is moving at. For any given
flow rate, velocity increases with smaller pipe
sizes. Thus, small pipe sizes have more friction
loss then do bigger pipe sizes, and therefore gobble
up more energy, increasing the cost of the
pumped water. At 2000 GPM, a 10-in pipe has
twice as much friction loss as a 12-inch pipe
has, while an 8-inch pipe has seven times more
loss.
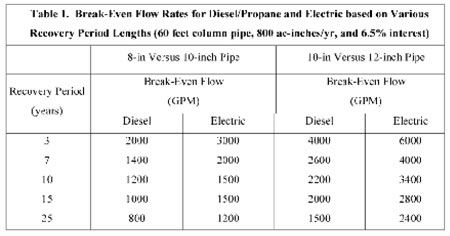
Besides the already mentioned factors of pipe
diameter and pipe length, the other significant
factors impacting the cost of the annual energy
lost from friction loss are (1) the cost of fuel and
(2) the amount of inches pumped. Since
diesel/propane is nearly twice as expensive as
electricity, there will be more incentive to go to
bigger pipe sizes if you use diesel or propane.
While bigger pipe sizes have less associated
operating costs, they obviously are more expensive.
In addition, if one moves up to a bigger column
pipe size, he also may face extra costs by
having to jump a size on the well and casing
used so that it will accommodate the larger diameter
of column pipe opted for.
“Pay now, or pay later” aptly describes the situation
– pay up front for a bigger size, or pay the
utility company later for added energy costs. The
break-even flow rate is the Gallon per Minute
amount at which the combined annual energy
costs plus the amortized fixed costs of the pipe
are equal between two pipe sizes. If the pump
flow rate exceeds the break-even flow rate, then
its cheaper to go with the larger sized pipe.
The original cost of a new well is a package
deal involving the steel column pipe of a size sufficient
for the flow rate, plus the cost of drilling
and casing a well that can handle the size of the
column pipe chosen. In our region, typical column
pipe length is 60 feet, while typical well and
casing length is normally about 100 feet. The
cost of both of these things is amortized to an
annual cost by using the interest rate of the
money involved and determining the number of
years desired to recovery the investment. Although
wells can have a system life of over 25
years, no banker would carry the paper that
long, so you might choose a recovery period of 5
to 7 years. As the fiscal recovery period increases,
the breakeven decreases. As indicated
earlier, the more expensive diesel/propane systems
will have bigger breakeven points then
electricity. Although the well is 100 feet deep,
pipe friction loss will occur in the 60-foot length
of column pipe.
Table 1 shows the break-even flow rates between
8- versus 10-inch and 10- versus 12- inch
pipe pairs for various return periods and type of
fuel used.
In summary, the size of column pipe you
choose is based on the flow rate of your well, but
other factors to consider include whether you
use diesel/propane or electricity. Δ
Dr. Joe Henggeler is Irrigation Specialist with
the University of Missouri Delta Center at
Portageville.